The Passive House concept represents today’s highest energy standard with the promise of slashing the heating energy consumption of buildings by an amazing 90%. Widespread application of the Passive House design would have a dramatic impact on energy conservation. Data from the U.S. Energy Information Administration shows that buildings are responsible for 48% of greenhouse gas emissions annually and 76% of all electricity generated by U.S. power plants goes to supply the Building Sector [Architecture 2030]. It has been abundantly clear for some time that the building sector is a primary contributor of climate-changing pollutants, and the question is asked: How do we best square our building energy needs with those of our environment and of our pocketbook? In the realm of super energy efficiency, the Passive House presents an intriguing option for new and retrofit construction; in residential, commercial, and institutional projects.
A Passive House is a very well-insulated, virtually air-tight building that is primarily heated by passive solar gain and by internal gains from people, electrical equipment, etc. Energy losses are minimized. Any remaining heat demand is provided by an extremely small source. Avoidance of heat gain through shading and window orientation also helps to limit any cooling load, which is similarly minimized. An energy recovery ventilator provides a constant, balanced fresh air supply. The result is an impressive system that not only saves up to 90% of space heating costs, but also provides a uniquely terrific indoor air quality.
A Passive House is a comprehensive system. “Passive” describes well this system’s underlying receptivity and retention capacity. Working with natural resources, free solar energy is captured and applied efficiently, instead of relying predominantly on ‘active’ systems to bring a building to ‘zero’ energy. High performance triple-glazed windows, super-insulation, an airtight building shell, limitation of thermal bridging and balanced energy recovery ventilation make possible extraordinary reductions in energy use and carbon emission.
Today, many in the building sector have applied this concept to design, and build towards a carbon-neutral future. Over the last 10 years more than 15,000 buildings in Europe – from single and multifamily residences, to schools, factories and office buildings – have been designed and built or remodeled to the passive house standard. A great many of these have been extensively monitored by the Passive House Institute in Darmstadt, analyzing and verifying their performance. Even governmental agencies have adopted passive house standards in their policy-making (read more about the EU Commission’s intent to implement the Passive House Standard.).
Performance Characteristics
- Airtight building shell ≤ 0.6 ACH @ 50 pascal pressure, measured by blower-door test.
- Annual heat requirement ≤ 15 kWh/m2/year (4.75 kBtu/sf/yr)
- Primary Energy ≤ 120 kWh/m2/year (38.1 kBtu/sf/yr)
In addition, the following are recommendations, varying with climate:
- Window u-value ≤ 0.8 W/m2/K
- Ventilation system with heat recovery with ≥ 75% efficiency with low electric consumption @ 0.45 Wh/m3
- Thermal Bridge Free Construction ≤ 0.01 W/mK
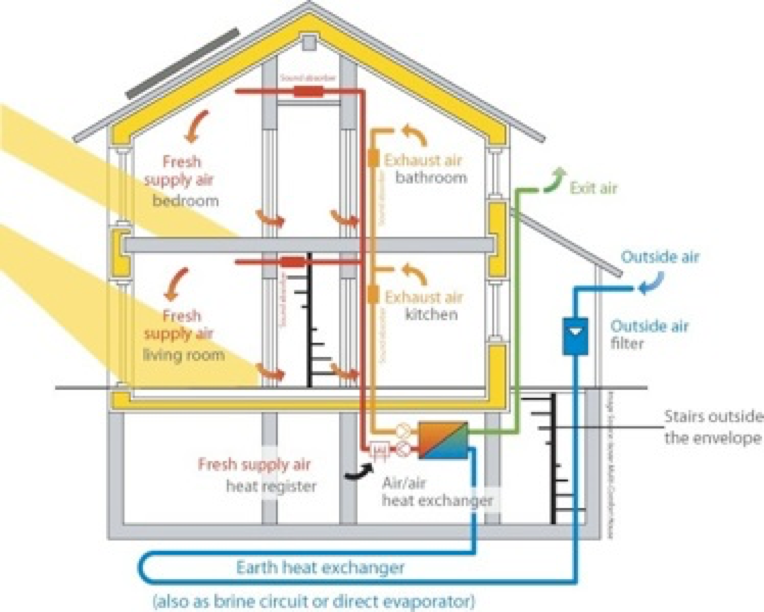
The building science research culminated in the development of the Passive House Planning Package (PHPP) which projects detailed heat load, heat loss, and primary energy usage for individual building parameters. The latest version of the PHPP also projects cooling, cooling loads, and latent cooling. Based on feedback from many detailed data logged buildings, the software is constantly refined and incorporates updated calculations for various climates around the world.
Terra-Petra Waterproofing Division is available for you water management and consulting services.
Contact us for further information.